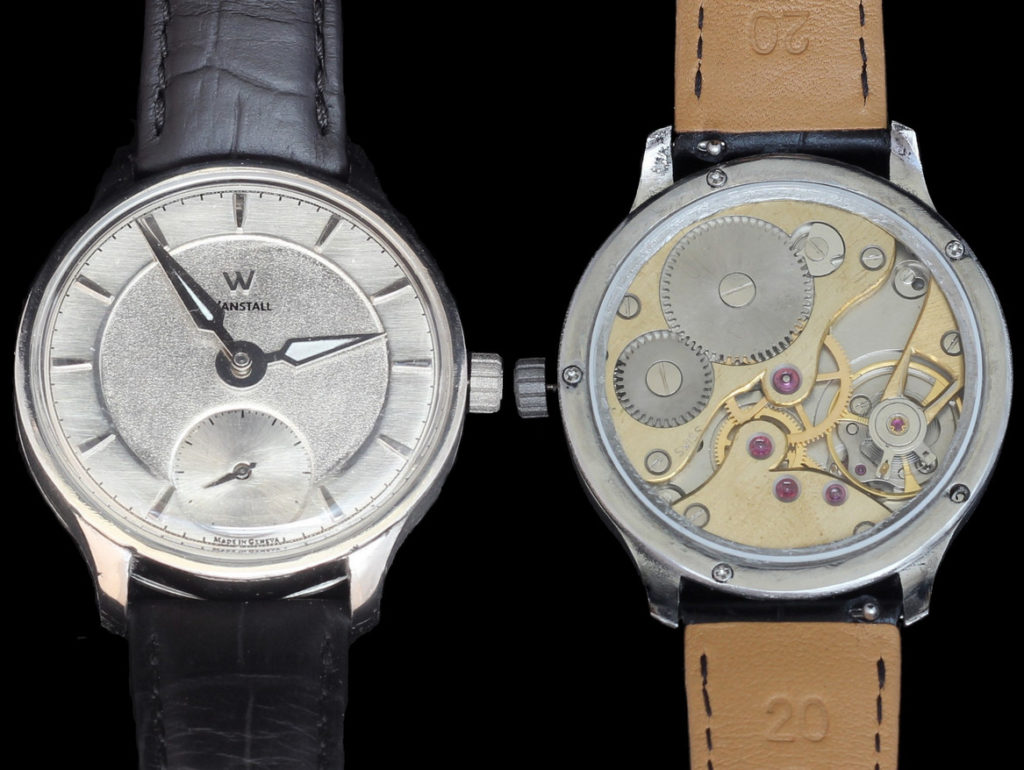
In October 2019 I started to work on the design and production of a watch, which I completed in April 2021, having worked on it roughly 300 hours. I have listed in the table below what I have done myself, what I have outsourced because I did not have the tools required, and the components that I bought. I ended up buying the movement, crystals and gaskets and either doing the rest myself or having my designs printed professionally. I believe this makes this watch comparable to any watch from a watch company that does not produce in-house movements.
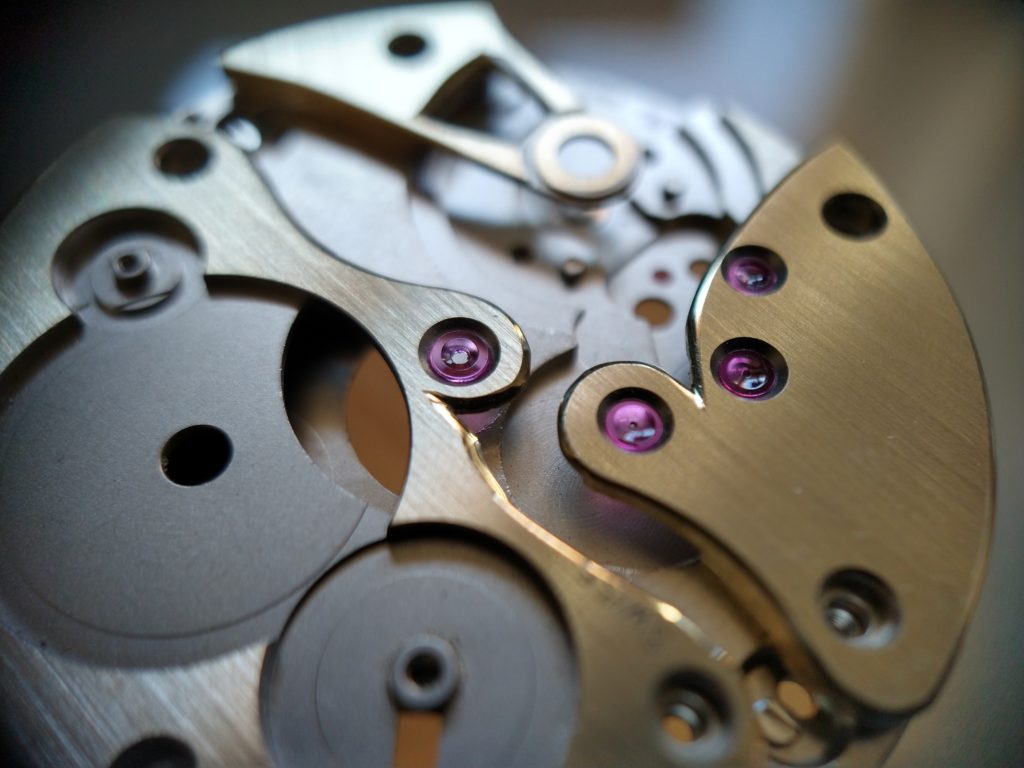
What I did
- Design the base dial
- Texture the base dial
- Design the printing on the dial
- Design the indices
- Finish the indices
- Design the logo
- Finish the logo
- Assemble all components of the dial
- Design the case
- Finish the case
- Re-finish the movement
- Service the movement
- Assemble the movement, dial and encase them
What I outsourced
- 3D printing the dial
- Pad printing on the dial
- 3D printing the indices
- 3D printing the hands
- 3D printing the case, caseback and crown
What I bought
- ETA 6498 movement
- Screws, gaskets and glasses
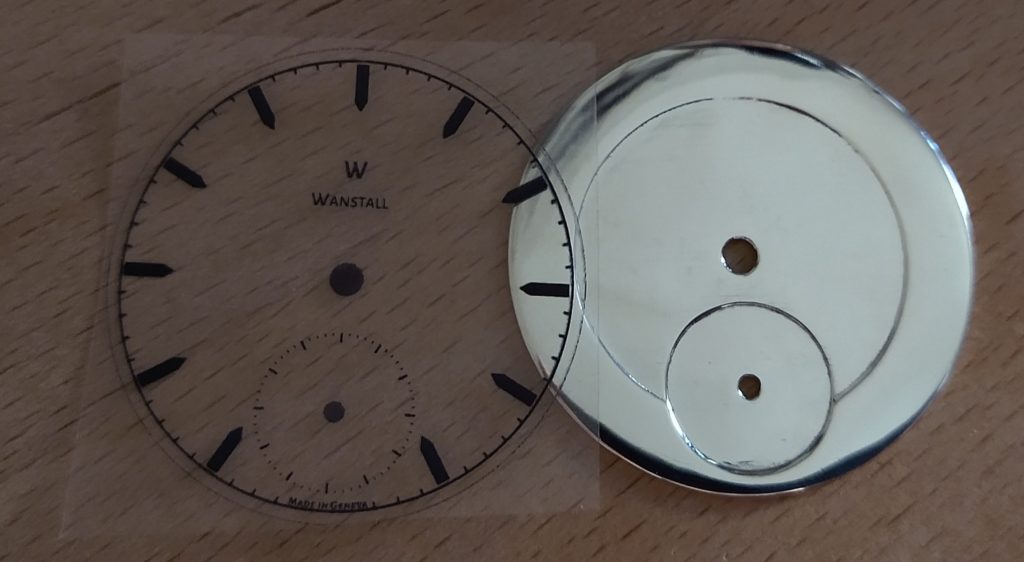
The number of steps in the process of creating the watch are quite large and I realized early on that I would need a system to organise the work on the different components, manage dependencies and track my progress. I chose to use a Gantt chart and the online TeamGantt website, but any Gantt chart software or even spreadsheet would work.
I used free software to design the vector graphics (BoxySVG) and 3D models (FreeCAD). I also used Blender to create 3D images.
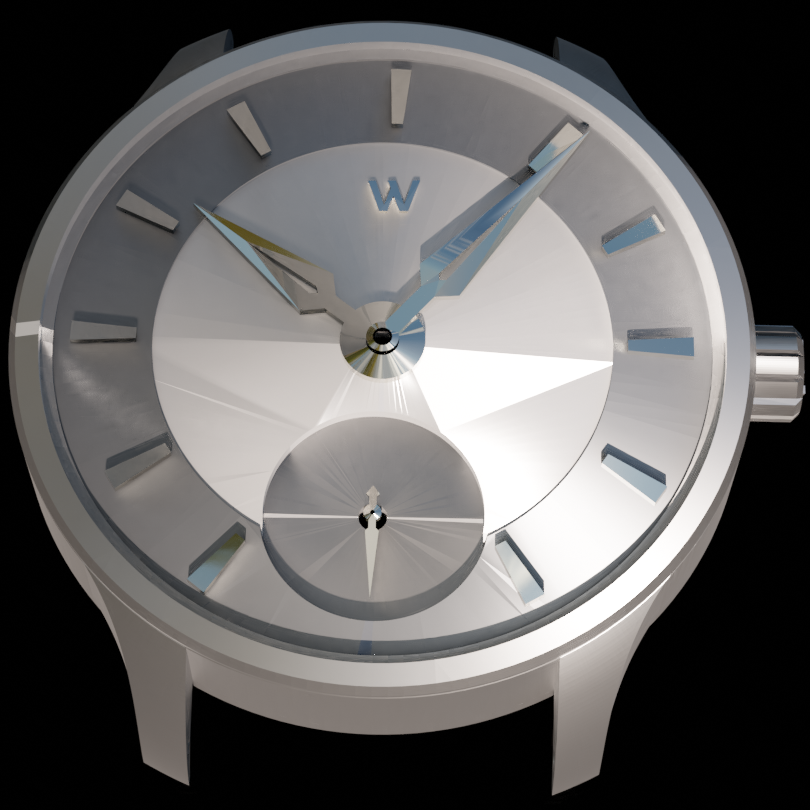